Bending Die Manufacturing
Jacky Technology (Dongguan) CO.,LTD CNC machining has become an indispensable technology in modern manufacturing. Its ability to produce high-precision, complex parts with efficiency and flexibility has made it a cornerstone of many industries. As technology continues to advance, CNC machining will likely play an even greater role in shaping the future of manufacturing.
Bending dies are essential tools in the metalworking industry, Jacky Technology (Dongguan) CO.,LTD used to shape sheet metal into desired forms through bending operations. The manufacturing of bending dies requires precision, expertise, and an understanding of the materials and processes involved. This article outlines the key steps and considerations in bending die manufacturing.
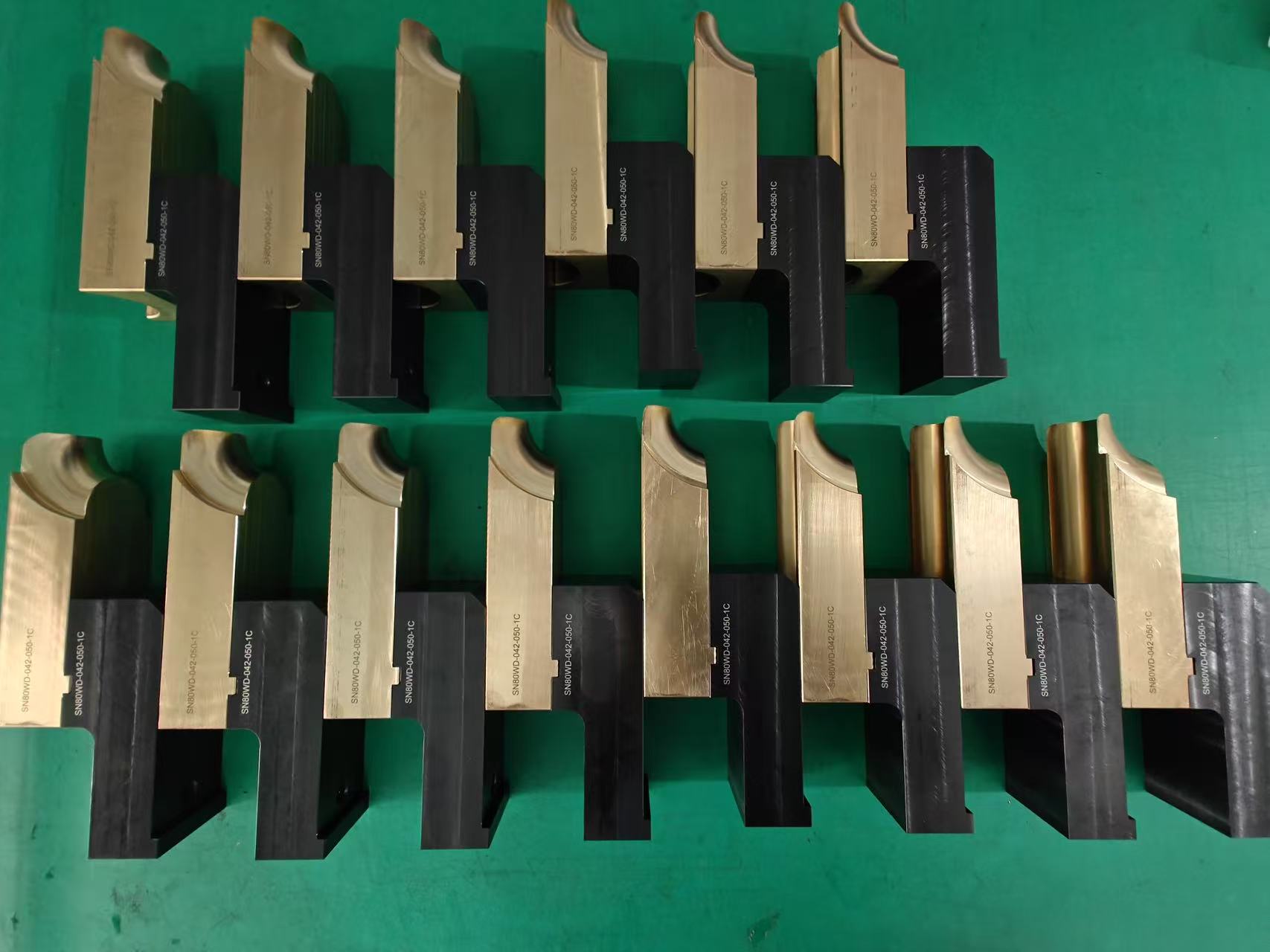
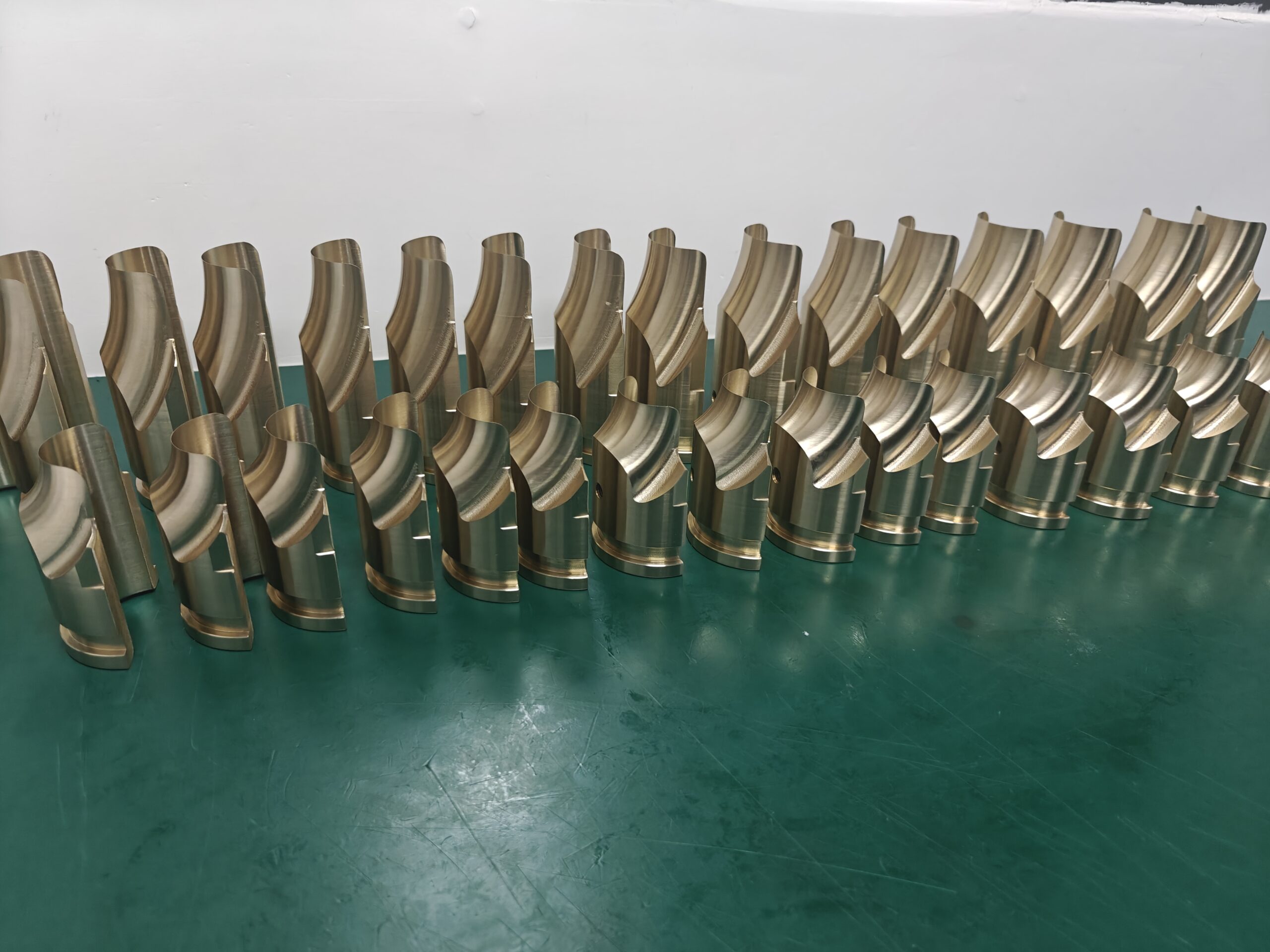
The first step in bending die manufacturing is the design phase. Engineers use CAD (Computer-Aided Design) software to create detailed blueprints of the die. The design must account for factors such as:
– The material properties of the workpiece (e.g., thickness, hardness, and elasticity).
– The desired bend angle and radius.
– The type of bending operation (e.g., V-bending, U-bending, or air bending).
– The press brake specifications (e.g., tonnage and bed length).
Material Selection
The choice of material for the bending die is critical to its performance and longevity. Common materials include:
– Tool Steel: High-carbon steels like D2 or A2 are widely used for their hardness and wear resistance.
– Carbide: For high-volume production or abrasive materials, carbide inserts may be used.
– Alloy Steels: These are often used for less demanding applications due to their lower cost.
Machining Processes
Once the design is finalized, the die is manufactured using various machining processes:
CNC Milling: Computer Numerical Control (CNC) milling machines are used to cut the die to precise dimensions.
Grinding: Surface grinding ensures the die has a smooth finish and accurate dimensions.
– EDM (Electrical Discharge Machining): For complex shapes or hard materials, EDM is used to erode the material with electrical sparks.
– Heat Treatment: The die is heat-treated to enhance its hardness and durability.
Surface Treatment
To improve wear resistance and reduce friction, the die may undergo surface treatments
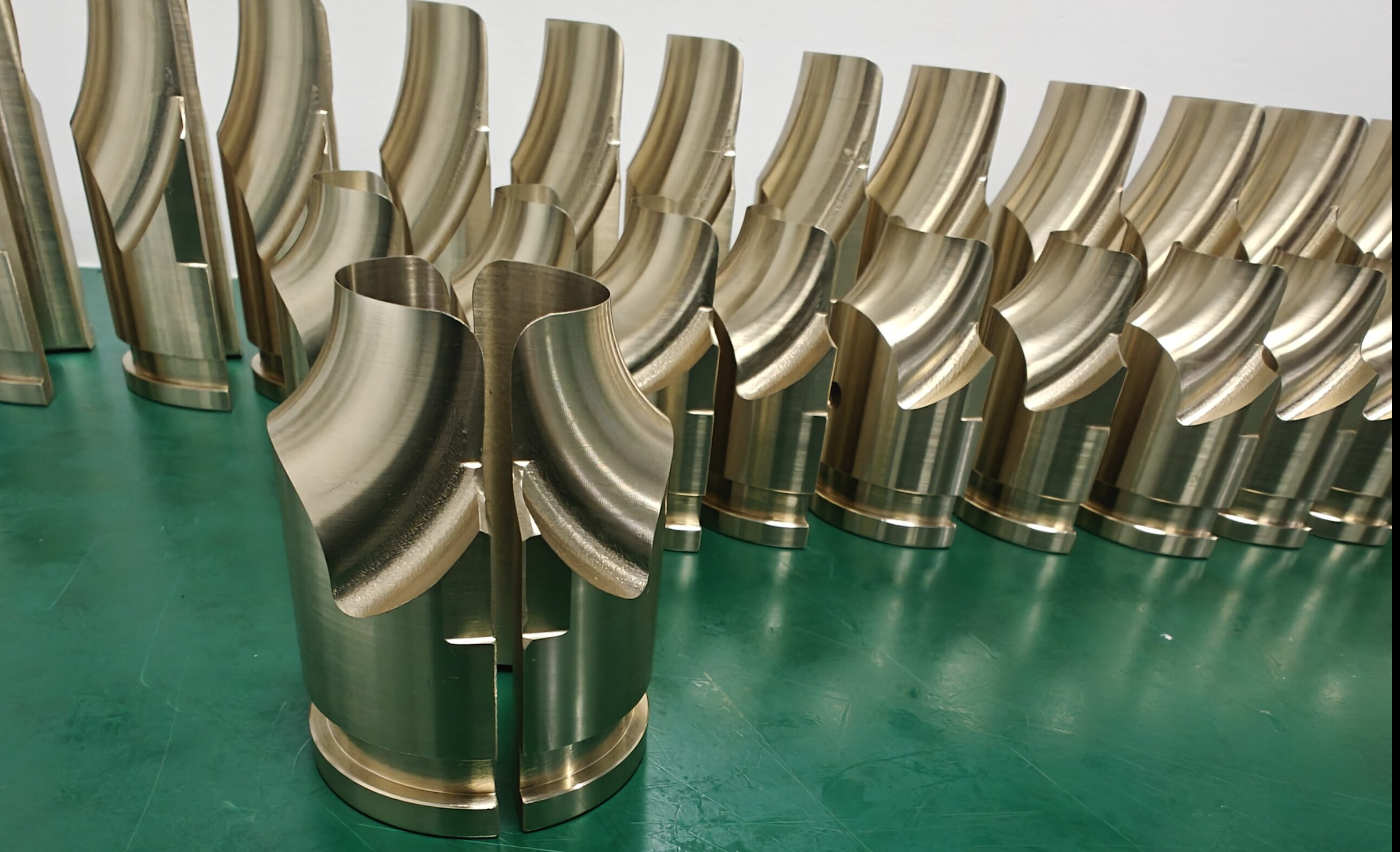
If you need precision mold component machining and CNC machining services or are looking for a suitable precision component machining factory, please choose Jac-Tec,Jac-Tec provides one-stop machining and production services for precision mold component and machining parts and assemblies for new energy, medical equipment, electronics .robotics, commercial equipment, and so on. You can conatct with project manager Maggie email: maggie@maqmtec.com Tel: +86 13632861056.
– Nitriding: A process that introduces nitrogen into the surface layer to increase hardness.
– Coating: Applying coatings like titanium nitride (TiN) or chromium nitride (CrN) can extend the die’s lifespan.
Quality Control
After manufacturing, the die undergoes rigorous quality control checks:
– Dimensional Inspection**: Using tools like CMM (Coordinate Measuring Machines) to ensure accuracy.
– Hardness Testing: To verify that the die meets the required hardness specifications.
– Trial Bending: Testing the die on a press brake to ensure it produces the desired bend.Maintenance and Repair
Proper maintenance is crucial to prolong the life of bending dies. Regular cleaning, lubrication, and inspection can prevent premature wear. If damage occurs, dies can often be repaired through welding, grinding, or re-coating.
Jacky Technology (Dongguan) CO.,LTD Bending die manufacturing is a complex process that requires a combination of advanced engineering, precise machining, and thorough quality control. By understanding the materials, processes, and considerations involved, Jacky Technology (Dongguan) CO.,LTD manufacturers can produce high-quality dies that meet the demands of modern metalworking